梳齒螺紋銑刀片表示方法
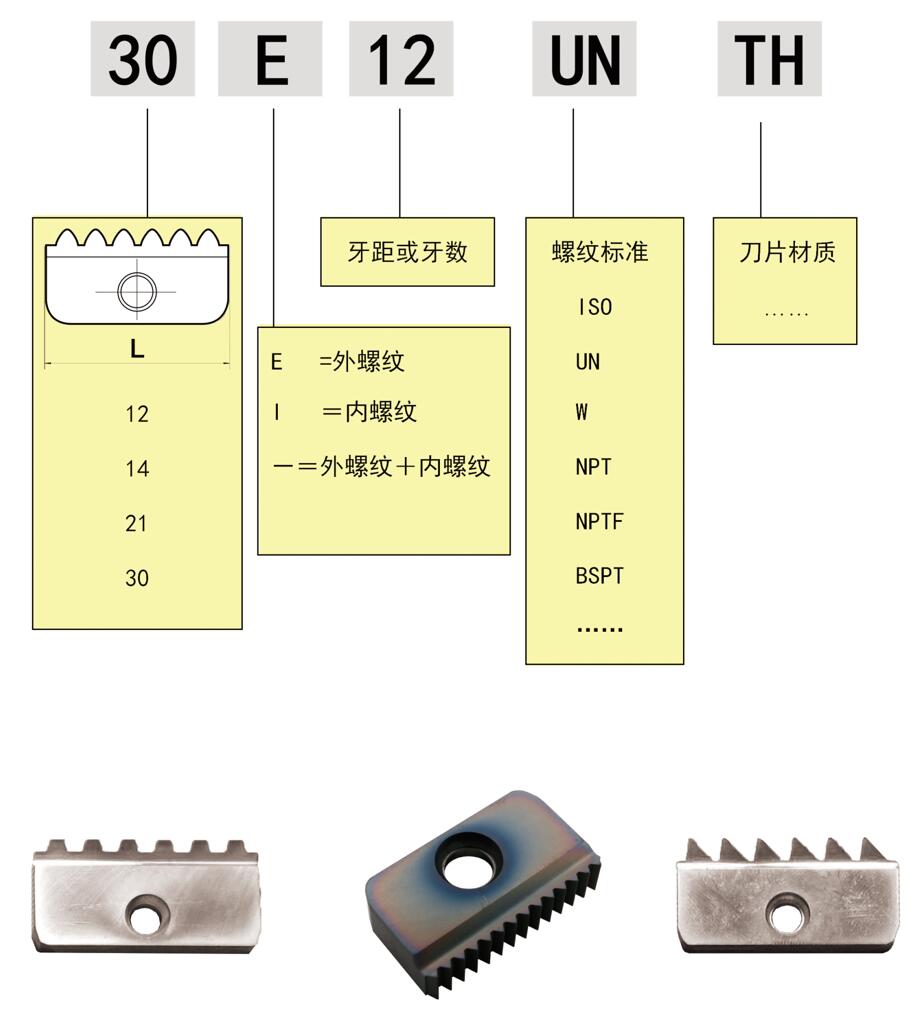
推薦切削參數(shù)表
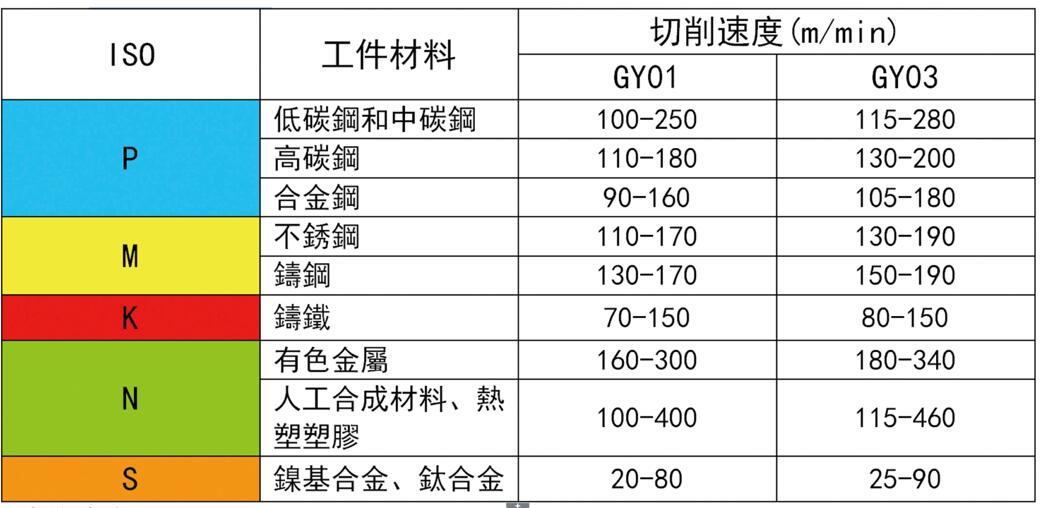
進給速度:0.05-0.15mm
銑削螺紋注意事項
大多數(shù)情況下剛開始使用時選擇中檔數(shù)值,對于硬度較高的材料,減低切削速度。
床孔加工刀桿懸伸度大時,請降低切削速度和進給速度至原來的20%~40% (取之于工件材料,牙距和懸伸量)。
對于螺距大(牙形不對稱)的必須分粗精銑,材質硬或彈性大、深徑比大的都需要分2-3刀進行加工,否則會出現(xiàn)振動大、表面品質差、塞規(guī)進不去等問題。在加工中還要注意螺紋 刀桿的伸出盡量短以增加剛性,減少振動,提高進給。
刀具選擇步驟
- 根據(jù)待加工螺距選擇刀片
- 選擇回轉直徑de小于被加工尺寸
- 對照上表將符合上面兩條件的刀具按最大刀具直徑選擇
螺紋銑削編程
在螺紋銳削的切入方法中,圓弧切入法、徑向切入法、切向切入法。我們推薦采用1/8 或1/4圓弧切入法,螺紋銑刀走過1/8或1/4螺距后,切線切進工件,然后再走360。整圓 切削插補一周,軸向移動一個導程,最后再走1/8或1/4螺距切出工件。
采用圓弧切入法,刀具切入,切出平衡,不留任何痕跡,不產生振動,即使是加工硬的 材料也如此。?
?
1 .螺紋銑削參數(shù)及計算公式
(1) .刀具轉速的計算
刀具的轉速等于機床主軸的轉速,即 n=1000v/nD7
式中:n—刀具轉速(r/min); v一刀具線速度(m/min); D刀一銑刀回轉直徑(包括刀片)(mm);
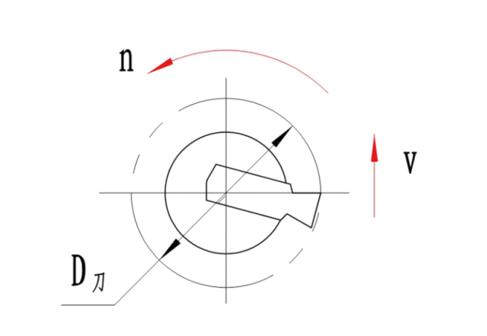
(2) .刀具徑向進給速度計算
刀具的徑向進給速度就是銑刀回轉直徑(包括刀片)
F1=fzn
式中:F1一刀具徑向進給速度(mm/min);
千一每刃每轉進給量(mm/r);
z一刀具切削刃數(shù);
(3) 刀具中心進給速度計算
大多數(shù)的CNC機床,在編程時要求采用刀具中心進給速度編程。刀具的進給速度由刀具 中心的進給速度的大小決定,而刀具中心的進給速度沒有直接給出,但可由刀具進給速度與 刀具中心的關系方程式求得。程式按刀具中心軌跡編寫,這種編程方法不考慮刀具半徑補償 和磨損抵消,程式簡單,修改方便。
加工外螺紋時的刀具中心進給速度,即
F2= F1 X (D+ D 刀)/D
式中:F2一刀具中心進給速度(mm/min); D一螺紋公稱直徑(螺紋大徑)(mm); 加工內螺紋時的刀具中心進給速度,即
F2= F1 X (D1- D 刀)/D1
式中:D1—螺紋小徑(mm); 在生產現(xiàn)場,未知小徑的情況下,可用螺紋公稱直徑 (螺紋大徑)簡便計算。
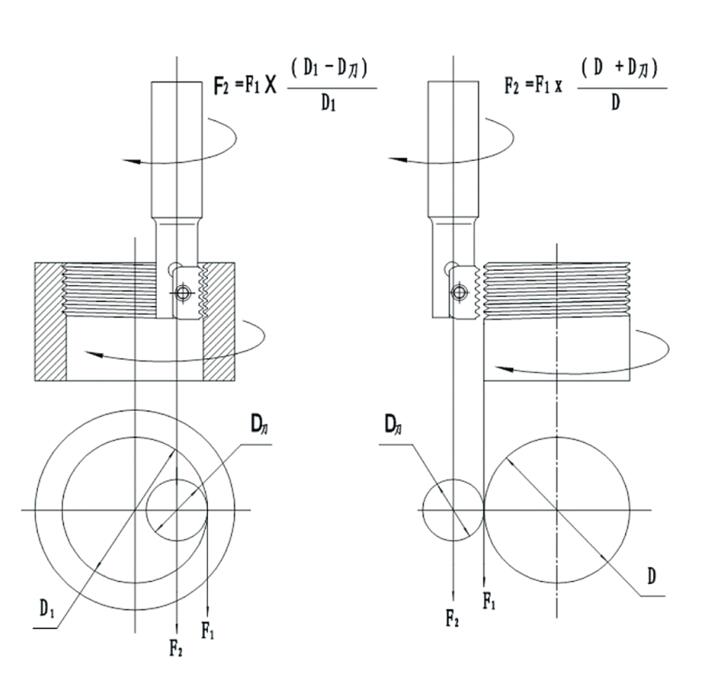
螺紋銑削通用程式
G90 GOO G54 G43 H1 XO YO Z10 S-
G00 Z-(螺紋深度)
G01 G91 G41 D1 X (A/2) Y- (A/2) ZO F-
G03 X (A/2) Y (A/2) R (A/2) Z (1/8 螺距)
G03 XO YO I- (A) JO Z (螺距)
G03 X- (A/2) Y (A/2) R (A/2) Z (1/8 螺距)
G01 G40 X- (A/2) Y- (A/2) Z0
G90 XO YO Z0
以上的數(shù)據(jù)是按理論的推算給出的,在實際螺紋銳削加工過程中,由于螺紋加工深度、 螺距大小、加工材料、冷卻條件等不同而有所變化。在加工中還要注意螺紋刀桿的伸出盡量 短以增加剛性,減少振動,提高進給。對于盲孔螺紋,為防止加工到孔底部時,加工部位被 切屑遮蓋,切屑堆積與刀具產生干涉,采用從孔底向外加工的走刀方向。
2.螺紋銑削編程實例
編制M25X1.5內螺紋程式,螺紋深度18mm,工件材料為45*;
根據(jù)螺紋大小,選擇刀具型號:ST90-21R1T21-B20,刀具回轉直徑①21mm; 刀片型號:2111.5IS0,材料牌號:GY03。
刀具線速度153m/min; 一片銑刀加工,每轉進給量0. 07mm/r ;
N10 G40 G80;
N20 G91 G28 Z0;
N30 M6 T1 ;
N40 G17 G54 G90 GO X0 Y0 M3 S2320;
N50 G43 H1 Z60;
N60 G01 Z-18.188 F5000 M08;
N70 G91 ;
N80 G41 D10 X1. Y1. Z0 F26;
N90 G03 X1. Y1. Z0. 188 IO J1.;
N100 G03 X0 Y0 Z1.5 I-2. J0;
N110 G03 X-1. Y1. Z0.188 1-1. J0;
N120 G01 G40 X-1. Y-1. Z0. F5000;
N130 G01 Z25.;
N140 G90 GO X0 Y0 Z50;
N150 G91 G28 Z0;
N160 M30;
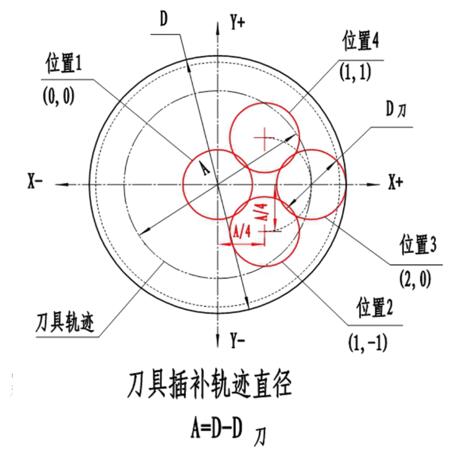